Ship anodes made of copper, aluminium & iron for antifouling systems
Marine Growth Prevention Systems, often referred to as antifouling systems, are systems for the prevention of microbial and organic surface growth, which prevent the adhesion and colonisation of microorganisms, algae, mussels and other marine organisms on ships, drilling platforms and other maritime structures.
This organic growth often causes blockages in pipework, seawater valves and other important parts of the ship's equipment. This requires time-consuming cleaning work and costly repairs to ensure the operational capability and safety of the ship.
There are various types of marine growth prevention systems, including electrolytic systems that prevent the growth of organisms through the controlled release of ions. Antifouling systems in which anodes made of copper and aluminium or copper and iron are used in pairs prevent organic fouling.
EKK supplies ship anodes for electrolytic antifouling systems with cofferdam flanges for use in sea chests, seawater filters or processing tanks. These anodes are always used in pairs – usually in the metal combinations aluminium/copper or iron/copper.
What are the advantages of antifouling systems?
- Reduced maintenance costs due to less frequent replacement of pipework
- Prevention of partial blockages, which lead to extremely high engine temperatures and increased fuel consumption
- Protection of equipment for fire protection, cooling and air conditioning systems that are operated with seawater
- Two systems in one – reducing biofouling and corrosion in pipework
- Automated process that requires minimal control by personnel
- Simple installation in sea chests or processing tanks
- Without the addition of chemicals
Ship anodes for sea chests, seawater filters & treatment tanks
Based on the electrolysis principle, EKK anodes are mounted in pairs (Cu/Al or Cu/Fe) in the sea chest or sea water filter. The copper anode releases ions during operation. This prevents so-called biofouling (biological contamination).
In addition, the aluminium anode produces ions that react with the seawater and form a layer on the inner surfaces of the pipes. This layer also acts as corrosion protection.
In piping systems made of copper-nickel materials, an iron anode is used instead of the aluminium anode. Here too, corrosion is reduced by the deposition of an oxide layer on the inner surfaces of the pipe.
By using EKK marine anodes, you not only reduce unwanted organic growth, but also prevent corrosion in the pipework system.
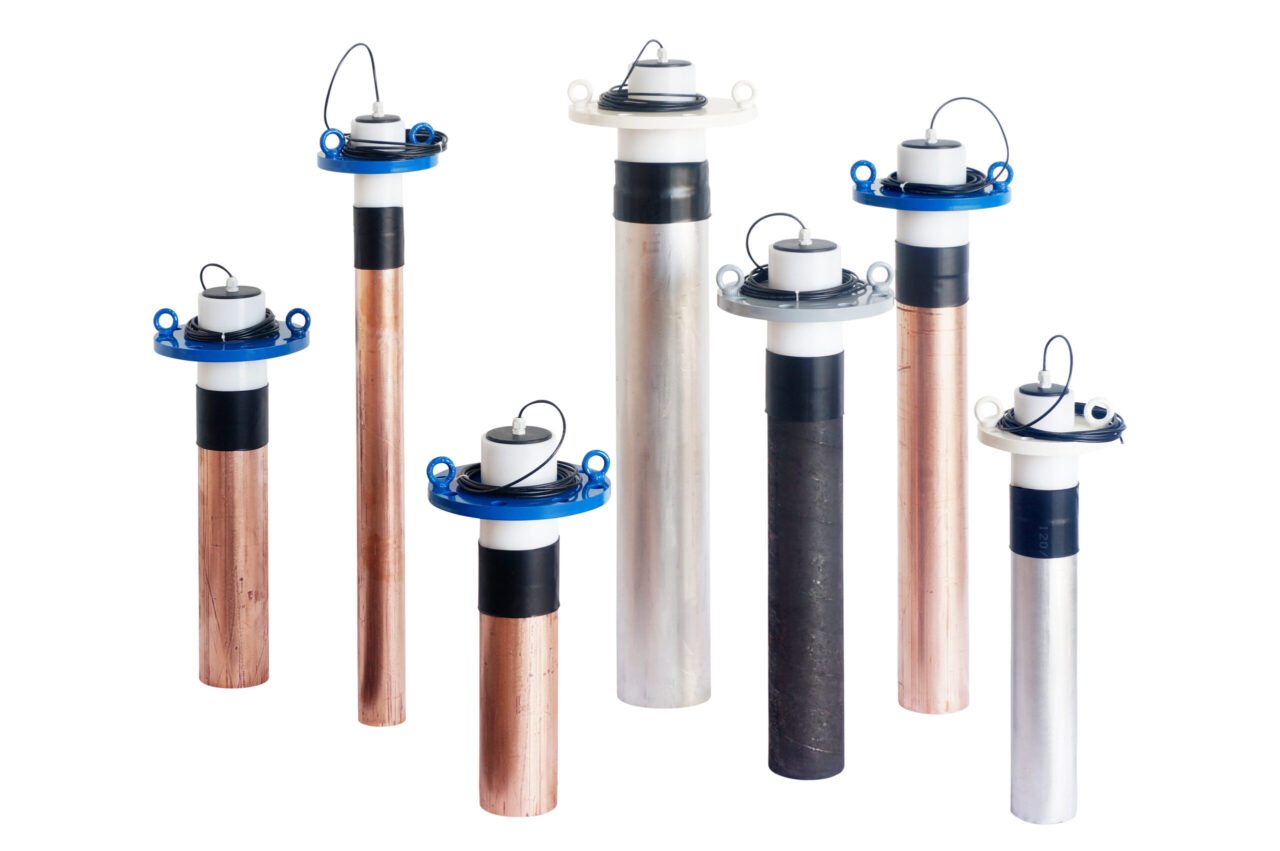
Certified quality with cofferdam anodes
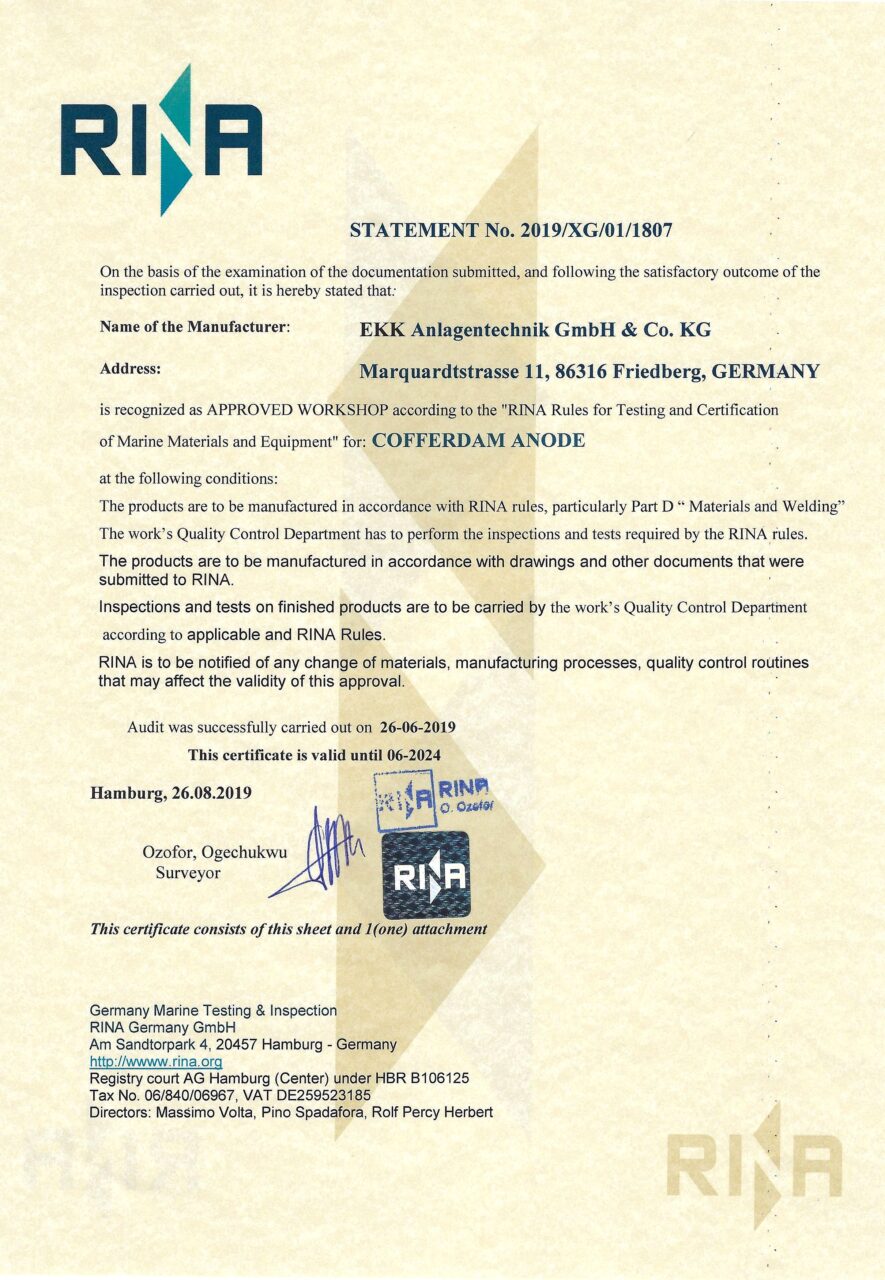
When using the cofferdam anodes, the germicidal effect of copper is utilised. The anodes with watertight cofferdam flanges are mounted in the sea chests and energised. This causes the copper anode to release copper ions. A second cofferdam anode made of iron or aluminium acts as a counter pole.
The quality of all our products is guaranteed by our proven ISO 9001 quality management system. In addition, we have acquired independent 3rd party certification from RINA GERMANY GMBH for the production of ship anodes. This certificate confirms that the RINA regulations for the testing and certification of marine accessories and equipment are complied with in the manufacture of products for the marine industry.
EKK ship anodes with cofferdam flanges are manufactured according to our production drawings. The quality testing of the ship anodes is based on the test specifications and test regulations of RINA.
With EKK ship anodes with cofferdam flanges, you are purchasing a product that meets the tested quality standards of various certification bodies in all aspects.
Are you looking for the right marine anode?
For a detailed description of the required ship anode, you will find a query drawing for ship anodes in the download area. Enter the relevant data so that we can offer the right ship's anode for you.
EKK ship anodes in the materials copper, aluminium and iron are usually available from stock in the common diameters 80 mm, 90 mm, 100 mm and 120 mm. The respective length is individually adapted to the corresponding installation situation.
The same applies to the design of the cofferdam flanges, which are constructed according to the given installation situation of the respective ship customers.